Giáo trình Dụng cụ cắt vật liệu kĩ thuật
Chọn vật liệu dao tiện định hình.
- Dao tiện định hình thường có biên dạng phức tạp, làm việc trong điều kiện cắt nặng nề, lực cắt lớn, nhiệt cắt lớn. Vì vậy, cần chọn vật liệu làm dao có độ cứng cao, độ bền nhiệt cao, độ bền cơ học và khả năng chống mòn tốt.
- Với vật liệu chi tiết gia công là thép 50, cần gia công đạt cấp chính xác IT12, độ nhẵn cấp 5, chọn vật liệu dao tiện định hình là thép gió P18, nó đáp ứng đầy đủ các yêu cầu trên.
Thép P18 có thể gia công các loại thép có b > 850 (N/mm2) và gang có độ cứng HB > 220.
Thành phần thép gió P18:
C(%) Cr(%) W(%) V(%)
0,7-0,8 3,8-4,4 17,5-19 1-1,4
- Thép gió có hàm lượng Vonfram cao làm cho thép gió có tính cứng nóng cao, cắt gọt với tốc độ cắt cao (2-4) lần thép cacbon dụng cụ, tốc độ cắt lớn nhất của dao thép gió là Vmax = 50 m/ph, khi nung giữ được độ cứng cao ở gần 6000C. Hàm lượng Crôm có tác dụng làm tăng độ thấm tôi.
Hàm lượng V làm tăng tính chống mài mòn và giữ cho hạt nhỏ khi tôi.
Sau khi tôi thép gió P18 có tổ chức:
Máctenxit +Ôtenít dư (30%)+Cac bit dư(15%)
Với độ cứng HRC 62 - 65
Tóm tắt nội dung tài liệu: Giáo trình Dụng cụ cắt vật liệu kĩ thuật
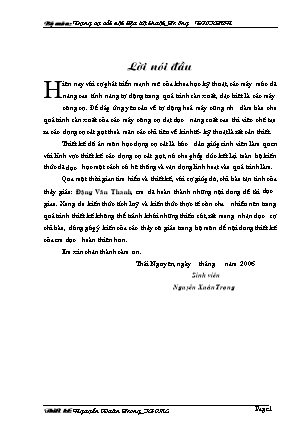
Lời nói đầu H iện nay với sự phát triển mạnh mẽ của khoa học kỹ thuật, các máy móc đã nâng cao tính năng tự động trong quá trình sản xuất, đặc biệt là các máy công cụ. Để đáp ứng yêu cầu về tự động hoá máy cũng như đảm bảo cho quá trình sản xuất của các máy công cụ đạt được năng suất cao thì việc chế tạo ra các dụng cụ cắt gọt thoả mãn các chỉ tiêu về kinh tế- kỹ thuật là rất cần thiết. Thiết kế đồ án môn học dụng cụ cắt là bước đầu giúp sinh viên làm quen với lĩnh vực thiết kế các dụng cụ cắt gọt, nó cho phép đúc kết lại toàn bộ kiến thức đã được học một cách có hệ thống và vận dụng linh hoạt vào quá trình làm. Qua một thời gian tìm hiểu và thiết kế, với sự giúp đỡ, chỉ bảo tận tình của thầy giáo: Đặng Văn Thanh, em đã hoàn thành những nội dung đề tài được giao. Xong do kiến thức tích luỹ và kiến thức thực tế còn chưa nhiều nên trong quá trình thiết kế không thể tránh khỏi những thiếu sót, rất mong nhận được sự chỉ bảo, đóng góp ý kiến của các thầy cô giáo trong bộ môn để nội dung thiết kế của em được hoàn thiện hơn. Em xin chân thành cảm ơn. Thái Nguyên, ngày tháng năm 2006 Sinh viên Nguyễn Xuân Trọng Phần i - Thiết kế dao tiện định hình Dao tiện định hình dùng để gia công những chi tiết định hình ở dạng sản xuất hàng loạt lớn hoặc hàng khối. Chúng bảo đảm độ đồng nhất về hình dáng và độ chính xác kích thước của cả loạt chi tiết gia công, năng xuất cắt cao, số lần mài lại cho phép lớn. Muốn vậy, khi thiết kế dao tiện định hình cần chọn vật liệu dao hợp lý, kết cấu dao hợp lý, tính kích thước biên dạng dao chính xác và đề ra những yêu cầu kỹ thuật chế tạo thật hợp lý. 1. Chọn vật liệu dao tiện định hình. - Dao tiện định hình thường có biên dạng phức tạp, làm việc trong điều kiện cắt nặng nề, lực cắt lớn, nhiệt cắt lớn. Vì vậy, cần chọn vật liệu làm dao có độ cứng cao, độ bền nhiệt cao, độ bền cơ học và khả năng chống mòn tốt. - Với vật liệu chi tiết gia công là thép 50, cần gia công đạt cấp chính xác IT12, độ nhẵn cấp 5, chọn vật liệu dao tiện định hình là thép gió P18, nó đáp ứng đầy đủ các yêu cầu trên. Thép P18 có thể gia công các loại thép có sb > 850 (N/mm2) và gang có độ cứng HB > 220. Thành phần thép gió P18: C(%) Cr(%) W(%) V(%) 0,7-0,8 3,8-4,4 17,5-19 1-1,4 - Thép gió có hàm lượng Vonfram cao làm cho thép gió có tính cứng nóng cao, cắt gọt với tốc độ cắt cao (2-4) lần thép cacbon dụng cụ, tốc độ cắt lớn nhất của dao thép gió là Vmax = 50 m/ph, khi nung giữ được độ cứng cao ở gần 6000C. Hàm lượng Crôm có tác dụng làm tăng độ thấm tôi. Hàm lượng V làm tăng tính chống mài mòn và giữ cho hạt nhỏ khi tôi. Sau khi tôi thép gió P18 có tổ chức: Máctenxit +Ôtenít dư (30%)+Cac bit dư(15%) Với độ cứng HRC 62 - 65 2. Chọn kích thước kết cấu dao tiện định hình. - Chọn theo hình dáng lớn nhất tmax của chi tiết gia công. Chiều cao hình dáng lớn nhất, xác định theo công thức: Với cấp chính xác thấp IT12, độ nhẵn cấp 5. Chọn dao tiện định hình tròn hướng kính gá thẳng có điểm cơ sở ngang tâm. Chọn điểm cơ sở ngang tâm là điểm 0 (Hình 1) Hình 1:Các điểm biên dạng chi tiết - Theo bảng 2 - 3, kích thước kết cấu của dao tiện định hình tròn có lỗ chốt là: Chiều cao hình dáng lớn nhất của chi tiết Kích thước dao tiện D d(H8) d1 bmax K r Dt d2 > 8...11 75 22 34 15 4 2 42 5 Hình 2: Kết cấu dao tiện định hình tròn ngoài có lỗ chốt 3. Chọn thông số hình học dao tiện định hình. + Góc sau a: Dao tiện định hình thường cắt với lớp phoi mỏng nên góc sau a được chọn lớn hơn so với dao tiện thường để tăng bền cho lưỡi cắt. - Với dao tiện định hình tròn a = 100á 120. Chọn a = 120 + Góc trước g: Phụ thuộc vào cơ tính của vật liệu gia công. - Theo bảng 2 - 4, với vật liệu chi tiết gia công là thép 50, có: sb = 640 N/mm2 , HB = 207 á 241. - Chọn g = 22o 4. Tính chiều cao hình dáng các điểm biểu diễn biên dạng dao. Hình 3: Sơ đồ tính chiều cao hình dáng dao tiện định hình tròn ngoài + Hoành độ: Biểu thị kích thước chiều trục của các điểm trên biên dạng lưỡi cắt của dao so với điểm cơ sở ngang tâm 0. + Đây là dao tiện định hình hướng kính gá thẳng nên kích thước chiều trục của các điểm biên dạng trên lưỡi cắt đúng bằng kích thước chiều trục của các điểm tương ứng trên chi tiết gia công : l1 = 9 ( mm ) l2 = 32- (7+9) = 16 ( mm ) l4 = 40- (7+9) = 24 ( mm ) l5 = 9 ( mm ) l6 = 9+7 = 16 ( mm ) + Tung độ: Biểu thị chiều cao hình dáng của các điểm biên dạng trên lưỡi cắt so với điểm cơ sở ngang tâm. + Các công thức tính: h = R.sina Bn = B - tn H = R.sin(a+g) tggon = H/Bn B = R.cos(a+g) tn = R - Rn Trong đó: a- góc sau tại điểm cơ sở ngang tâm g- góc trước tại điểm cơ sở ngang tâm R- bán kính của dao ứng với điểm cơ sở ngang tâm Rn- bán kính của dao ứng với điểm thứ n trên biên dạng lưỡi cắt tn- chiều cao hình dáng điểm thứ n biên dạng dao theo mặt trước tn- chiều cao hình dáng điểm thứ n biên dạng dao tính theo tiết diện vuông góc với mặt sau. Tính chiều cao hình dáng cho các điểm 0; (3,4); (1,2,5,6) trên biên dạng dao tương ứng với các điểm 0; (3,4); (1,2,5,6) trên biên dạng chi tiết. *Chiều cao hình dáng điểm 0. h = 37,5.sin120 = 7,8 H = 37,5.sin(120+220) = 21 B = 37,5.cos(120+220) = 31 *Chiều cao hình dáng điểm 3,4. B3,4 = B - t3,4 Với a = r.sing = 8,5.sin220 = 3,18 sing3,4 = a/r1 = 3,18/10 = 0,318 ị cosg3,4 = 0,948 và g3,4 = 18,50 b = r.cosg = 8,5.cos220 = 7,88 C3,4 = r1.cosg3,4 = 10.0,948 = 9,48 ị t3,4 = 9,48 - 7,88 = 1,6 ị B3,4 = 31 - 1,6 = 29,4 tgg03,04 = H/B3,4 = 21/29,4 = 0,714 ị g03,04 = 35,50 R3,4 = t3,4 = 37,5 - 36,2 = 1,3 Ta có: g03,04 = g + a + b03,04 ị b03,04 = 35,50 - (220 + 120) = 1,50 Mặt khác: a3,4 = a + g - g3,4 + b03,04 ị a3,4 = 170 *Chiều cao hình dáng điểm 1,2,5,6. sing1,2 = a/r1,2 = 3,18/17,5 = 0,182 ị cosg1,2 = 0,983 và g1,2 = 10,50 C1,2 = r2.cosg1,2 = 17,5.0,983 = 17,2 ị t1,2 = 17,2 - 7,88 = 9,32 ị B1,2 = 31 - 9,32 = 21,68 tgg01,02 = H/B1,2 = 21/21,68 = 0,97 ị g01,02 = 440 R1,2 = t1,2 = 37,5 - 30,2 = 7,3 Ta có: g01,02 = g + a + b01,02 ị b01,02 = 440 - (220 + 120) = 100 Mặt khác: a1,2 = a + g - g1,2 + b01,02 ị a1,2 = 33,50 5.Xác định cung tròn thay thế. Biên dạng chi tiết gia công có đoạn cong là 1 cung tròn đối xứng trong phạm vi nửa đường tròn. Xác định bán kính Rtt của cung tròn thay thế theo công thức: tgb = t / x Rtt = x / sin2b Trong đó: x -chiều rộng của cung hình dáng dao t -chiều cao hình dáng dao ị x = 9 mm t = 7,3 Do đó: tgb = 7,3/9 = 0,811 ị b = 390 Rtt = 9 / sin2.390 = 9,2 6. Xác định dung sai kích thước biên dạng dao của dao tiện định hình. Độ chính xác hình dáng kích thước của chi tiết gia công phụ thuộc vào dộ chính xác hình dáng kích thước biên dạng của dao. Vì vậy cần xác định dung sai kích thước biên dạng dao chặt chẽ. Trong quá trình gia công chi tiết định hình có thể coi dao như là chi tiết trục (bị bao). Vì vậy nên bố trí trường dung sai kích thước biên dạng dao như đối với trục cơ sở, nghĩa là sai lệch trên bằng không và sai lệch dưới âm. Bố trí như vậy, sai số biên dạng dao sẽ tạo ra sai số có thể sửa được trên biên dạng chi tiết. Chi tiết gia công bằng dao tiện định hình đạt cấp chính xác IT12, chọn cấp chính xác của dao tiện định hình cao hơn 3 cấp là IT9. - Dựa vào cấp chính xác và kích thước biên dạng của dao Theo bảng 2 - 8, được các sai lệch kích thước biên dạng dao. + Dung sai chiều cao hình dáng các điểm biên dạng dao: t1 = 1,3-0,025 t2 = 7,3-0,036 + Dung sai kích thước chiều trục các điểm biên dạng dao: l1 = 9-0,036 l4 = 24-0,052 l2 = 16-0,043 l5 = 9-0,036 l6 = 16-0,043 - Dung sai bán kính cung tròn thay thế lấy bằng 1/5 dung sai đường kính của điểm cơ sở ngang tâm (F17-0,18): R9,2-0,04 - Dung sai các kích thước góc (tính bằng phút) lấy bằng trị số dung sai nhỏ nhất của chiều cao hình dáng dao (tính bằng mm): 25’ - Để bảo đảm gá dao chính xác và bảo đảm biên dạng dao không đổi sau mỗi lần mài lại, cần quan tâm đến dung sai kích thước chiều cao mài dao H. Tính theo công thức: dh = (mm) dH = (mm) Trong đó: R- bán kính của dao tại điểm cơ sở ngang tâm a- góc sau tại điểm cơ sở ngang tâm g- góc trước tại điểm cơ sở ngang tâm da - dung sai của góc a, độ d(a+g) -dung sai của góc a+g, độ 7.Xác định các phần phụ của lưỡi cắt và vẽ biên dạng toàn bộ lưỡi cắt. + Để tăng bền cho lưỡi cắt, lấy thêm đoạn lưỡi cắt phụ a = 2 mm + Để tạo lượng dư xén mặt đầu, lấy c = 1 mm, với góc j1 = 200 + Để chuẩn bị cho nguyên công cắt đứt lấy: b = 4 mm t = 6 mm b1 = 1 mm j = 150 + Để giảm ma sát khi cắt, đoạn lưỡi cắt 23 được vát nghiêng 1 góc j0 = 10 8. Điều kiện kỹ thuật của dao tiện định hình. 8.1. Vật liệu phần cắt : Thép gió P18 Vật liệu thân dao : Thép gió P18 8.2. Độ cứng sau nhiệt luyện. - Phần cắt : HRC 62 á 65 - Phần thân dao : HRC 30 á 40 8.3. Độ nhẵn - Mặt trước và mặt sau dao thép gió bằng cấp 8 ( Ra = 0,63 mm ) - Các mặt chuẩn định vị và kẹp chặt: Đạt cấp 8 ( Ra = 0,63 mm ) - Các mặt còn lại đạt cấp 6 ( Ra = 2,5 mm ) 8.4. Sai lệch các góc mài sắc: 25’ 9. Gá kẹp dao tiện định hình. Dao tiện định hình được định vị và kẹp chặt trong gá kẹp dao thích hợp. Yêu cầu của gá kẹp là phải bảo đảm định vị dao tốt đúng với sơ đồ tính toán, phải điều chỉnh tốt, kẹp chặt chắc chắn, ổn định và có tính công nghệ tốt, chế tạo và lắp ghép dễ dàng. Với kết cấu dao tiện định hình tròn ngoài có lỗ chốt, chọn gá kẹp dao thể hiện trên hình 2.29, được sử dụng trên máy tiện, máy tiện Rơvonve. Hình 4: Gá kẹp dao Dao được định vị trên bulông đỡ 1 và được kẹp chặt nhờ đai ốc kẹp 4 và chốt 2. Gá kẹp loại này có hai cơ cấu điều chỉnh mũi dao ngang tâm máy. Cơ cấu điều chỉnh thô gồm: Vít điều chỉnh 8, chốt 9, quạt điều chỉnh 6. Cơ cấu điều chỉnh tinh là ống lệch tâm 4. Khi quay ống lệch tâm 4 mũi dao được nâng lên hoặc hạ xuống so với trục của chi tiết gia công. Vít kẹp 5 để kẹp chặt ống lệch tâm. phần ii-Thiết kế dao chuốt rãnh then Dao chuốt là một loại dụng cụ cắt có năng xuất cao, thường dùng để gia công những bề mặt định hình trong và ngoài. Sau khi chuốt, bề mặt gia công có thể đạt độ chính xác cấp 8 á 7 v ... máy chuốt phải lớn hơn lực chuốt Pmax Để đảm bảo độ bền kéo cho dao cần thoả mãn điệu kiện: F : Diện tích tiết diện nguy hiểm ở đầu kẹp hay ở rãnh răng cắt thô thứ nhất. - Theo bảng 3 - 19, có: F = 300 mm2 đ - Theo bảng 3 - 29, có: đ đ Thoả mãn độ bền kéo. 19. Điều kiện kỹ thuật của dao chuốt rãnh then. a, Vật liệu: Thép P18. b, Độ cứng sau khi nhiệt luyện: - Phần răng và phần định hướng sau đạt: HRC 62 á 65 - Phần định hướng trước: HRC 60 á 62 - Phần đầu dao: HRC 40 á 47 c, Độ nhẵn bề mặt: - Cạnh viền của răng sửa đúng: Cấp 9 ( Ra = 0,32 ) - Mặt trước, mặt sau của răng, các bề mặt định hướng: Cấp 8 ( Ra = 0,63 ) - Mặt đáy răng, mặt ngoài của đầu dao, côn chuyển tiếp:Cấp 7 (Ra =1,25 ) - Các bề mặt không mài: Cấp 6 ( Ra =2,5 ). d, Chiều rộng cạnh viền trên răng sửa đúng f = 0,05á 0,2mm Trên răng cắt, chiều rộng cạnh viền không vượt quá 0,05mm e, Sai lệch cho phép chiều sâu rãnh chứa phoi: Không được vựơt quá +0,3 mm f, Sai lệch tổng cộng chiều dài của dao: Không được vượt quá ±5 mm g, Sai lệch bước răng cho phép trong phạm vi ± (0,2á 0,5) mm h, Sai lệch giới hạn chiều cao răng cắt và răng sửa đúng không vượt quá: ± 0,02mm (do lượng nâng của răng cắt thô SZ > 0,08mm) i, Dung sai chiều rộng lưỡi cắt của răng cắt và răng sửa đúng: Lấy bằng 1/3 dung sai chiều rộng rãnh then, trường dung sai phân bố về phía âm (sai lệch trên bằng 0) -0,016 j,Sai lệch giới hạn của góc: - Góc trước: ±10 - Góc sau: ±30’ k, Khắc nhãn hiệu trên cổ dao: - Đường kính lỗ chuốt : - Vật liệu dao chuốt : Thép gió P18 - Số hiệu dao chuốt : - Tên nhà máy chế tạo : Phần III-Xác định chế độ cắt I. Chọn dụng cụ cắt. 1. Chọn vật liệu dụng cụ cắt. Vì dao tiện có kích thước nhỏ, dùng trong các máy tự động, máy chuyên dùng,...thường chế tạo nguyên con bằng thép gió. Ngoài ra để tiết kiệm vật liệu quí, dao tiện thường được chế tạo theo kết cấu hàn mảnh dao. + Vật liệu phần cắt. Để tăng năng xuất cắt và chất lượng bề mặt gia công chọn vật liệu phần cắt theo bảng 4-2 là hợp kim cứng T15K6. Chọn mảnh dao theo bảng 4-7. + Vật liệu phần thân: Thép 45 2. Chọn kiểu dụng cụ cắt. - Theo bảng 4-22, chọn dao tiện ngoài đầu thẳng có: j = 45o ; B = 16 ; H = 25 L = 160 ; a = 10 3. Chọn kích thước chung của dụng cụ cắt. + Chọn tiết diện ngang của thân dao: - Theo bảng 4-24, tiết diện thân dao theo chiều cao tâm máy. B.H = 16.25 + Chọn chiều dài dao: - Theo bảng 4-25, chọn dao tiện đối với bàn dao có 4 chỗ kẹp: L = 160 ( mm ) 4. Chọn hình dáng mặt trước của dụng cụ cắt. Hình dáng mặt trước của dao tiện được chọn phụ thuộc vào vật liệu phần cắt, với dao hợp kim cứng. Theo bảng 4-27, chọn hình dáng mặt trước của dao phẳng, có cạnh vát âm. 5. Chọn thông số hình học phần cắt của dao. Góc sau a và góc trước g được chọn phụ thuộc vào vật liệu gia công, lượng chạy dao và hình dáng mặt trước. - Theo bảng 4 -32, có: g = 15o ; a = 12o Góc nghiêng chính j, góc nghiêng phụ j1 và góc nâng l được chọn phụ thuộc vào điều kiện làm việc cụ thể. - Theo bảng 4 - 33, chọn: j = 450 - Theo bảng 4 - 34, chọn: j1 = 250 - Theo bảng 4 - 35, có: l = 50 Chọn lưỡi cắt nối tiếp có dạng cung tròn. Với S < 0,2 mm/vòng đ Chọn r = 2 ( mm ) 6. Chọn trị số độ mòn cho phép của phần cắt. Trị số độ mòn cho phép của phần cắt được chọn phụ thuộc vào kiểu dao tiện, vật liệu gia công và điều kiện làm việc cụ thể. - Theo bảng 4 - 37, có: Độ mòn cho phép: hs = 0,8 ( mm ) 7. Chọn tuổi bền của dụng cụ cắt. Tuổi thọ Số lần mài lại cho phép + 1 Tuổi bền = Tuổi bền của dao được xác định theo công thức: - Theo bảng 4-39, Với dao tiện ngoài, kích thước tiết diện thân dao B.H = 20.30 đ Số lần mài lại cho phép = 21 Tuổi thọ của dao = 22 giờ Tuổi bền = (giờ) đ Tuổi bền = 60 ( phút ) II. Chọn chiều sâu cắt t. Chiều sâu cắt được chọn phụ thuộc vào lượng dư gia công h và yêu cầu về độ nhẵn bề mặt gia công. - Lượng dư gia công khi tiện được tính theo công thức: Trong đó: D : Đường kính của chi tiết trước khi gia công : D = 40 ( mm ) Do : Đường kính của chi tiết sau khi gia công : D = 36 ( mm ) đ Với h = 2 để nâng cao năng xuất cắt chọn t = h, nên chỉ cắt một lần hết lượng dư. III. Chọn lượng chạy dao S. 1. Xác định lượng chạy dao để bảo đảm độ bền thân dao. Để bảo đảm độ bền thân dao, lượng chạy dao được tính theo công thức sau: ( mm/vòng) (*) Trong đó: W : Mô đun chống uốn của tiết diện thân dao ( mm3 ) B : Chiều rộng thân dao ở tiết diện nguy hiểm. H’ : Chiều cao thân dao ở tiết diện nguy hiểm. đ : ứng suất cho phép của tiết diện thân dao. Thân dao thường làm bằng thép cácbon nên: t : Chiều sâu cắt: t = 2 mm. L : Tầm với ( Khoảng cách từ mũi dao đến tiết diện nguy hiểm ). Thường : L = ( 1 á 1,5 )H Chọn : L = 1,2.H = 1,2.25 = 30 ( mm ). Cpz : Hệ số để tính lực cắt Pz. xpz : Số mũ xét tới ảnh hưởng của t tới lực cắt Pz. - Theo bảng 4 - 54, có: Kpz : hệ số hiệu chỉnh xét tới ảnh hưỏng của các nhân tố tới lực cắt Pz . Tính Kpz theo công thức: : Hệ số hiệu chỉnh xét tới ảnh hưởng của vật liệu gia công đến Pz . - Theo bảng 4 - 55, có: - Theo bảng 4 - 56, có: đ Thay các hệ số vừa xác định được vào công thức ( * ), được: 2. Xác định lượng chạy dao để bảo đảm độ bền cho cơ cấu chạy dao. Để bảo đảm cơ độ bền cho cấu chạy dao, lượng chạy dao được tính theo công thức sau: ( mm/vòng ) ( ** ) Trong đó: : Trị số lớn nhất cho phép của lực chiều trục tác lụng lên cơ cấu chạy dao. Với máy tiện ren vít 1K62, xác định được: t : Chiều sâu cắt: t = 2 ( mm ) Cpx : Hệ số để tính lực cắt Pz . xpx : Số mũ xét tới ảnh hưởng của chiều sâu cắt t đến Px . ypx : Số mũ xét tới ảnh hưởng của lượng chạy dao S đến Px . - Theo bảng 4 - 54, có: Kpx : Hệ số hiệu chỉnh xét tới ảnh hưởng của các nhân tố đến lực cắt Px Tính Kpx theo công thức : Với: - Theo bảng 4 - 56, có: đ Thay các hệ số vừa tính được vào công thức ( ** ) ta được: 3.Xác định lượng chạy dao để bảo đảm độ cứng vững của chi tiết gia công Để bảo đảm độ cứng vững chi tiết gia công lượng chạy dao được xác định theo công thức sau: ( mm/vòng ) ( *** ) Trong đó : K : Hệ số phụ thuộc vào cách gá chi tiết trên máy. K = 3 ( chi tiết kẹp một đầu trên mâm cặp) E : Mô đun đàn hồi của vật liệu chi tiết gia công, với thép E = 20.104 (N/mm2) J : Mô men quán tính tiết diện ngang của chi tiết gia công. D : Đường kính chi tiết gia công. : Độ võng cho phép của chi tiết gia công. Tiện thô: = 0,2 á 0,4 đ chọn = 0,3 ( mm ). L : Chiều dài của chi tiết gia công, không kể đoạn nằm trong mâm cặp của máy, L = 40 mm Cpy : Hệ số để tính lực Py xpy : Số mũ xét tới ảnh hưởng của chiều sâu cắt t đến Py. ypy : Số mũ xét tới ảnh hưởng của lượng chạy dao S đến Py. - Theo bảng 4 - 54, có : Kpy :Hệ số hiệu chỉnh xét tới ảnh hưởng của các nhân tố tới lực cắt Py. : Hệ số hiệu chỉnh xét tới ảnh hưởng của vật liệu gia công đến Py. - Theo bảng 4 - 55, có : - Theo bảng 4 - 56, có : đ Thay các hệ số trên vào ( *** ), được : 4. Xác định lượng chạy dao để đảm bảo độ bền của mảnh dao. Để đảm bảo độ bền của mảnh dao, lượng chạy dao xác định theo công thức sau: (mm/vòng) trong đó: ẵPzẵ- lực lớn nhất cho phép tác dụng lên mảnh dao hợp kim cứng. theo bảng 4-57, với hợp kim T15K6 : ẵPzẵ= 6600 - 10%.6600 = 5940 ị 5. Xác định lượng chạy dao thực của máy Sm. Từ các lượng chạy dao đã xác định được ở trên: So sánh với các lượng chạy dao dọc của máy 1K62, chọn được lượng chạy dao thực của máylà: IV. Xác định tốc độ cắt V và số vòng quay n. 1. Xác định tốc độ cắt V. Khi tiện ngoài thì tốc độ cắt được tính theo công thức sau: Trong đó: : Tốc độ cắt ứng với tuổi bền của dao T (m/min) t : Chiều sâu cắt. S : Lượng chạy dao (mm/vòng). : Hệ số để tính tốc độ cắt. m : chỉ số tuổi bền : Số mũ xét tới ảnh hưởng của t đến V. : Số mũ xét tới ảnh hưởng của S đến V. - Theo bảng 4 - 62, có : m = 0,2 : Hệ số hiệu chỉnh xét tới ảnh hưởng của các nhân tố tới tốc độ cắt V Trong đó : : Hệ số hiệu chỉnh xét tới ảnh hưởng của khả năng công nghệ tới tốc độ cắt V . - Theo bảng 4 - 59, có : : Hệ số hiệu chỉnh xét tới ảnh hưởng của cơ tính vật liệu gia công tới tốc độ cắt V. - Theo bảng 4 - 63, có : - Theo bảng 4 - 64, có : Thay các hệ số trên vào biểu thức của ta được : Thay vào biểu thức tính , có: 2. Xác định số vòng quay n. Số vòng quay lý thuyết được tính theo công thức: ( vòng/min ) So sánh với số vòng quay thực tế của máy, có: Chọn số vòng quay Vậy tốc độ cắt thực được xác định : V. Tính lực cắt. Các thành phần lực cắt khi tiện được tính theo công thức : + Với đ + Với đ + Với đ VI. Kiểm nghiệm chế độ cắt theo động lực và mô men máy. Chế độ cắt đã xác định ở trên phải thoả mãn những điều kiện sau: Pz ≤ [Pz] Trong đó: : Lực tiếp tuyến: V : Tốc độ cắt: V = 188,4 ( m/min ) : Công suất động cơ điện của máy. h : Hiệu suất của máy: D : Đường kính phôi: D = 40 ( mm ) : Mô men xoắn cho phép của trục chính. [Pz] - theo bảng 4 - 57, có [Pz] = 5940 Vậy ta có : Vậy chế độ cắt được xác định như trên đều thoả mãn. VII. Tính thời gian máy To. Trong đó: L : Chiều dài cần gia công của chi tiết: L = 40 (mm) y : Lượng ăn tới của dao. : Lượng vượt quá của dao, thường chọn y1 = 1 á 3 ( mm ) đ Chọn y1 = 2 ( mm ) i : Số lần cắt: i = 1 S : Luợng chạy dao: S = 0,34 n : Số vòng quay trong 1 phút của phôi: n = 1500 ( vòng/min ) đ tài liệu tham khảo [1] - Phạm Trung Chính, Nguyễn Mạnh Lân, Khâu Xuân Lương, Bùi Chính Nghĩa: Giáo trình vật liệu học_ĐHKTCN. [2] - PTS Trần Hữu Đà, TH.S Nguyễn Văn Hùng, TH.S Cao Thanh Long: Cơ sở chất lượng của quá trình cắt. [3] - Trịnh Khắc Nghiêm: Thiết kế đồ án môn học nguyên lý và dụng cụ cắt. [4] - PGS.TS Ninh Đức Tốn: Dung sai và lắp ghép. mục lục Trang Lời nói đầu 1 Phần I - thiết kế dao tiện định hình.......................... 2 Phần II - thiết kế dao chuốt rãnh then.................. 11 Phần III - xác định chế độ cắt....................................... 27
File đính kèm:
giao_trinh_dung_cu_cat_vat_lieu_ki_thuat.doc